Roller or spray procedures are frequently used for industrial surface coating production processes. Depending on the object, various technologies are used during production, for instance cup gun nozzles, automatic spray units and also highly complex roller lines. Painting processes are often process-controlled and run in combination with painting and drying equipment. Remmers Industrielacke will help you choose your individual coating system and provide in-depth system planning competence.
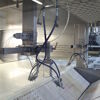
Spray machine
Spray machines can be used as single solutions or in combination with matching pre-treatment, cleaning, drying and conveyor systems as a complete painting line. To ensure a constantly high level of quality, precise setting of the following parameters is necessary when spray painting on a painting system: Supply pump pressure, mixing thinner and viscosity, material pressure, pump type and transmission, nozzle/air flap/setting angle, atomiser pressure, pistol type/number/distance and speed, system feed and application quantity.
Casting application
Curtain coating machines are used to apply fluid media onto flat materials, in particular lacquers and emulsions. They are also used for glues and adhesives, and for solvent-based and solvent-free coating systems. Also, they are highly suitable for problematic high-viscosity media, a high level of pigments, watery media and radiation curing systems.
- Casting film that is free of streaks and cracks thanks to the patented casting system
- Very small application quantities and tolerance-free cast film
- Fast cleaning thanks to modular components
- Flexible thanks to optional pumps and filling systems
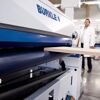
Roller application
Roller painting is used to apply circulation-capable coating agents from above onto one side of flat work pieces. In this process, the coating agent is transferred from a rotating rubber roller onto the workpiece surface. The work piece is moved through the roller machine on a sub-construction on a conveyor belt. Belt speed and application roller speed run at the same speed (feed). The required lacquer application quantities can be set via the adjustable gap between the application roller and the dosing roller. Also, the speed and direction of rotation (forwards - reverse) of the dosing rollers can be regulated separately. This allows the application quantities to be regulated more finely. There may be several coating rollers installed in a painting system for multi-layer, colourless or coloured lacquers. In addition to the roller application machines for applying stains and lacquers, painting systems also include drying and curing equipment.
Certification of the eco Institute
Our multi-layer UV system structure for parquet flooring, comprising the hydro-UV-primer, the UV-acrylic special primer, the UV-SIS-primer and the UV-acrylic parquet top coat, underwent an ecological product test by the eco Institute and then certified. All the limits defined in the test criteria were satisfied. This primarily involves emission and active content analyses.
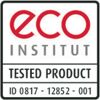
Highlight: Direct and digital printing structures
We have state-of-the-art technologies and technical expertise in the field of direct and digital printing structures. Printing machines in existing flat lines can be integrated into printing machines. A direct printing machine instead of the painting roller in the continuous production process rounds off the technological performance capability.
In addition to almost infinite possibilities in the digital printing field, there is also a wide range of design freedom and individualisation in the direct printing field. This means that various décors and also solid colours can be realised. The result is absolutely homogeneous and opaque surfaces also for small application quantities - in contrast to spray units.